MINING INDUSTRY DRILL BITS
MINING INDUSTRY TRICONE AND DIAMOND PDC DRILLING BITS
Penetration and wear are the two key elements of consistent drilling.
There are 3 main categories: soft, medium and hard formation drill bits.
- Soft formation rock bits are used in unconsolidated sands, clays, soft limestone, red beds and shale, etc.
- Medium formation bits are used in calcites, dolomites, lime stones, and hard shale.
- Hard formation bits are used in hard shale, calcites, mudstones, cherty limestone and hard and abrasive formations.
PDC DRILL BITS
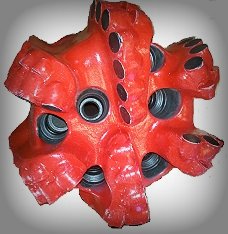
PDC bits are also known as fixed cutters because, unlike the tricone bit, there is no movement relative to the bit head. PDC bits shear rock with diamond faced pdc cutters affixed to tungsten carbide.
PDC cutters are created with high heat and high pressures. This creates a polycrystalline diamond compact. PDC cutters come in a variety of thicknesses for applications ranging from mining to oilfield.
PDC bits are used extensively in directional drilling. Directional drilling is used effectively in inland and offshore oil drilling, and natural gas drilling.
Fixed cutter bits are dull graded in the same way as tricones using the IADC Dull Grading
Classification System.
PDC drill bits, or fixed cutters, come in either :
Steel body fixed cutters are made from a high alloy steel. These bits can sometimes be repaired and may be good for multiple runs, depending on the application.
Because steel is better able to withstand high impact, steel body bits are often designed with higher blade stand-off and cutter exposure, thus increasing ROP.
In applications of high fluid volume or high sand, matrix body bits offer longer life and multiple bit runs.
Cost is a major factor in drilling a well. Because tungsten carbide is more expensive than steel and matrix bodies generally contain more cutters, matrix is generally more expensive.
HOW PDC CUTTERS ARE MADE
PDC cutters are made using a combination of high heat and high pressure. Man made diamonds can be grown in 5-10 minutes. Because of this diamond content, a fixed cutter bit may also be known as a diamond drill bit.
High heat plus pressure creates a polycrystalline diamond compact.
Cutters are made from a carbide substrate and diamond grit. High heat of around 2800 degrees and high pressure of approximately 1,000,000 psi forms the compact. A cobalt alloy is also present and acts as a catalyst to the sintering process. The cobalt helps bond the carbide and diamond.During the cooling process, the tungsten carbide shrinks at a rate of 2.5 times faster than the diamond. Controlling this stress, as with most aspects of PDC cutter design, is called Intellectual Property, and manufacturers rarely, if ever, share their secrets
COMMON DIAMOND DRILL BIT PDC CUTTER SIZES
PDC cutters are created with high heat and high pressures. This creates a polycrystalline diamond compact. PDC cutters come in a variety of thicknesses for applications ranging from mining to oilfield.
PDC bits are used extensively in directional drilling. Directional drilling is used effectively in inland and offshore oil drilling, and natural gas drilling.
Fixed cutter bits are dull graded in the same way as tricones using the IADC Dull Grading
Classification System.
PDC drill bits, or fixed cutters, come in either :
- matrix or
- steel body.
Steel body fixed cutters are made from a high alloy steel. These bits can sometimes be repaired and may be good for multiple runs, depending on the application.
Because steel is better able to withstand high impact, steel body bits are often designed with higher blade stand-off and cutter exposure, thus increasing ROP.
In applications of high fluid volume or high sand, matrix body bits offer longer life and multiple bit runs.
Cost is a major factor in drilling a well. Because tungsten carbide is more expensive than steel and matrix bodies generally contain more cutters, matrix is generally more expensive.
HOW PDC CUTTERS ARE MADE
PDC cutters are made using a combination of high heat and high pressure. Man made diamonds can be grown in 5-10 minutes. Because of this diamond content, a fixed cutter bit may also be known as a diamond drill bit.
High heat plus pressure creates a polycrystalline diamond compact.
Cutters are made from a carbide substrate and diamond grit. High heat of around 2800 degrees and high pressure of approximately 1,000,000 psi forms the compact. A cobalt alloy is also present and acts as a catalyst to the sintering process. The cobalt helps bond the carbide and diamond.During the cooling process, the tungsten carbide shrinks at a rate of 2.5 times faster than the diamond. Controlling this stress, as with most aspects of PDC cutter design, is called Intellectual Property, and manufacturers rarely, if ever, share their secrets
COMMON DIAMOND DRILL BIT PDC CUTTER SIZES
ROCK BITS
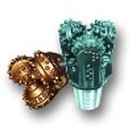
Also known as roller cone bits or two or TriCone bits, rock bits have two/three moving heads. Button bits have tungsten carbide inserts while tooth bits have steel teeth.
Much consideration goes into rock bit design, such as which bearing type to use.
There are primarily four (4) types of bearing designs used in TriCone drilling bits:
Rock bits adhere to the same API standards as PDC bits.
The continuous discovery of new natural gas reserves throughout the world is responsible for a dramatic increase in drilling activity. Unlike traditional drilling where only a vertical well is required to tap into the pay zone, natural gas production involves using unconventional drilling methods. The most common method is to drill horizontally into the gas bearing shale formations in order to capture more gas than ever before using traditional methods. For example , it is not uncommon for the horizontal well to reach out over 4000m.
Much consideration goes into rock bit design, such as which bearing type to use.
There are primarily four (4) types of bearing designs used in TriCone drilling bits:
- 1.) STANDARD OPEN BEARING ROLLER BIT: On these bits the cones will spin freely. This type of bit has a front row of ball bearings and a back row of roller bearings.
- 2.) STANDARD OPEN BEARING ROLLER BIT FOR AIR DRILLING: Cones are similar to #1, but have air injection directly to the cones to cool the bearings. Air flows into the cone through the passage ways inside the pin. (Not for mud applications)
- 3.) SEALED BEARING ROLLERS BITS These bits have an O-Ring seal with a grease reservoir for bearing cooling. The seals acts as a barrier against mud and cuttings to protect the bearings
- 4.) JOURNAL BEARING ROLLER BITS These bits are strictly oil/grease cooled with nose bearings, O-Ring seal and a race for maximum performance.
Rock bits adhere to the same API standards as PDC bits.
The continuous discovery of new natural gas reserves throughout the world is responsible for a dramatic increase in drilling activity. Unlike traditional drilling where only a vertical well is required to tap into the pay zone, natural gas production involves using unconventional drilling methods. The most common method is to drill horizontally into the gas bearing shale formations in order to capture more gas than ever before using traditional methods. For example , it is not uncommon for the horizontal well to reach out over 4000m.
TUNGSTEN CARBIDE INSERT DESIGN
Button bit inserts fall in two classifications: chisel and conical.
Chisel inserts are more aggressive than conical, and some designs employ a mixture of both.
Conical inserts are more domed in appearance and are used to grind formations that are more abrasive and are higher in compressive strength.
Tungsten carbide inserts are individually manufactured and then press fit into pre-drilled holes in the cone of the bit.
FLUID CIRCULATION
All rock drill bits require some type of fluid circulation. Drilling fluid may consist of water or oil, air, or foam. The circulation of drilling fluid serves several purposes:
*Clears away cuttings so new geological formations can be drilled
*Stabilizes the borehole wall
*Cleans and cools the bit
Button bit inserts fall in two classifications: chisel and conical.
Chisel inserts are more aggressive than conical, and some designs employ a mixture of both.
Conical inserts are more domed in appearance and are used to grind formations that are more abrasive and are higher in compressive strength.
Tungsten carbide inserts are individually manufactured and then press fit into pre-drilled holes in the cone of the bit.
FLUID CIRCULATION
All rock drill bits require some type of fluid circulation. Drilling fluid may consist of water or oil, air, or foam. The circulation of drilling fluid serves several purposes:
*Clears away cuttings so new geological formations can be drilled
*Stabilizes the borehole wall
*Cleans and cools the bit
DRAG BITS
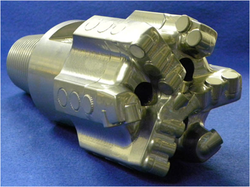
Used to drill softer geological formations and shallower depths, drag bits are economical. The tips, or wings, are affixed with tungsten carbide and come in either a step drill bit or chevron type bit.All tungsten carbide tips are silver soldered to the bit wing by a special process to insure a strong bond that will not shear or break when drilling through hard rock.
WELL WORKOVER BITS
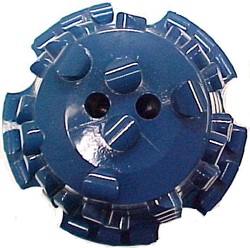
Workover bits are used to either complete a newly drilled well or to "work over" an existing well. Specialized manufacturers making reliable, cost-effective well workover bits.
Another option for drilling cement and plugs is a mill bit. To learn more about the various applications suitable for the workover mills.
Another option for drilling cement and plugs is a mill bit. To learn more about the various applications suitable for the workover mills.
DTH Hammer Bits
------------------------------------------------------------------------------------------------------------------------------------------------------------------
Type of ball/journal bearings implemented in drill bits:
- Standard open bearing roller bit
- Standard open bearing roller bit, air-cooled
- Standard open bearing roller bit with gauge protection which is defined as carbide inserts in the heel of the cone
- Sealed roller bearing bit
- Sealed roller bearing bit with gauge protection
- Journal sealed bearing bit
- Journal sealed bearing bit with gauge protection
How to find appropriate drill bits:
IADC Codes make it easier for drillers to describe what kind of rock bit they are looking for to the supplier.
First Digit:
1, 2, and 3 designate STEEL TOOTH BITS with 1 for soft, 2 for medium and 3 for hard formations.
4, 5, 6, 7 and 8 designate TUNGSTEN CARBIDE INSERT BITS for varying formation hardness with 4 being the softest and 8 the hardest.
Second Digit:
1, 2, 3 and 4 are further breakdown of formation with 1 being the softest and 4 the hardest.
Third Digit:
This digit will classify the bit according to bearing/seal type and special guage wear protection as follows:
Fourth Digit:
The following letter codes are used in the fourth digit position to indicate additional features:
A. Air Application
R. Reinforced Welds
C. Center Jet
S. Standard Steel Tooth
D. Deviation Control
X. Chisel Insert
E. Extended Jet
Y. Conical Insert
G. Extra Gage Protection
Z. Other Insert Shape
J. Jet Deflection
IADC Codes make it easier for drillers to describe what kind of rock bit they are looking for to the supplier.
First Digit:
1, 2, and 3 designate STEEL TOOTH BITS with 1 for soft, 2 for medium and 3 for hard formations.
4, 5, 6, 7 and 8 designate TUNGSTEN CARBIDE INSERT BITS for varying formation hardness with 4 being the softest and 8 the hardest.
Second Digit:
1, 2, 3 and 4 are further breakdown of formation with 1 being the softest and 4 the hardest.
Third Digit:
This digit will classify the bit according to bearing/seal type and special guage wear protection as follows:
Fourth Digit:
The following letter codes are used in the fourth digit position to indicate additional features:
A. Air Application
R. Reinforced Welds
C. Center Jet
S. Standard Steel Tooth
D. Deviation Control
X. Chisel Insert
E. Extended Jet
Y. Conical Insert
G. Extra Gage Protection
Z. Other Insert Shape
J. Jet Deflection
google-site-verification: google231c230fc8f05942.html